
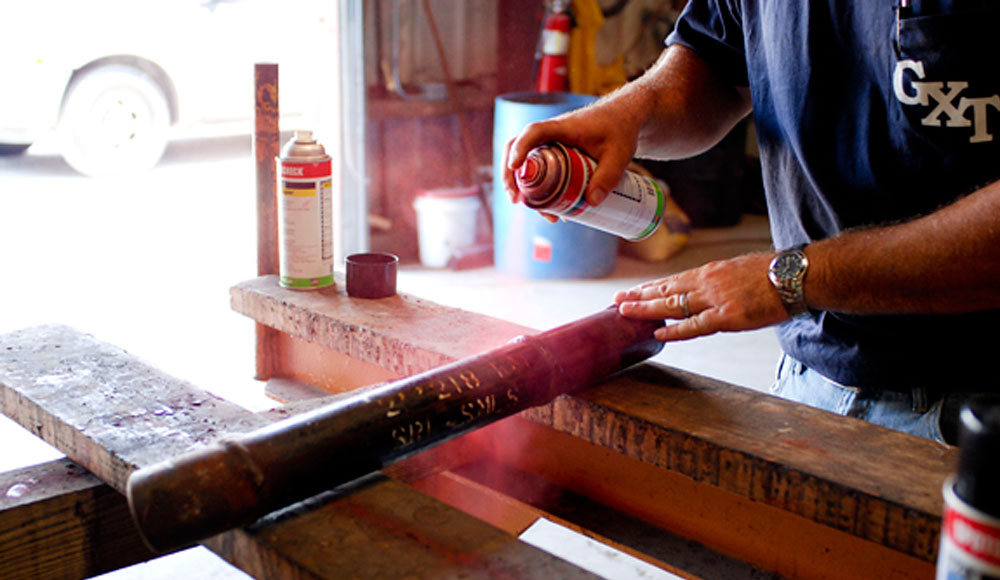
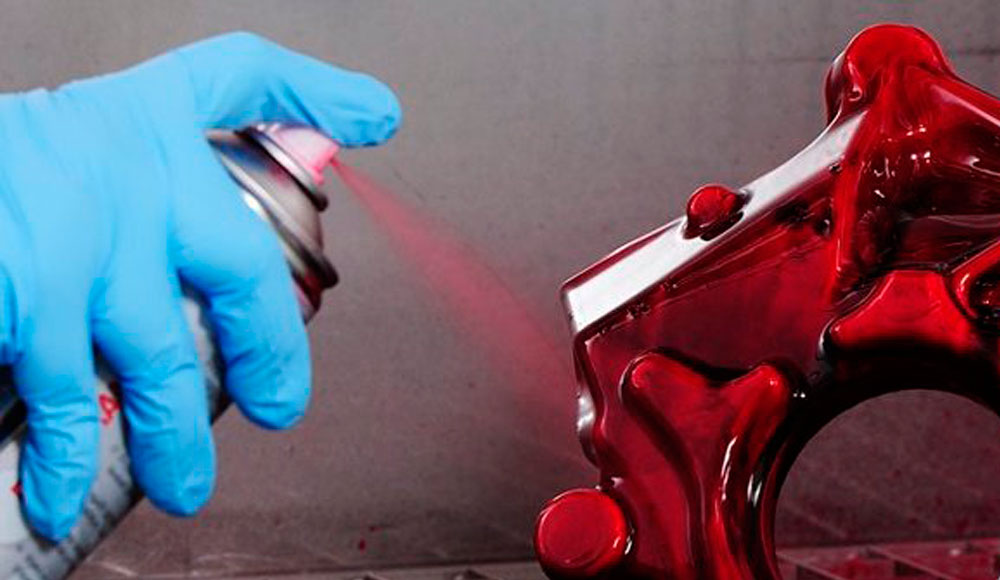
Application Principles
The principle of dye penetrant inspection method; is based on the capillary effect that low surface tension fluid penetrates clean and dry surface breaker continuities. Penetrant; can be applied by dipping, spraying etc. Once sufficient penetration time has been allowed, excess penetrants are removed and a developer is applied. The inspection is carried out under ultraviolet or white light, depending on the type of dye used.
Ultramat has lots of certificate and certified products to meet the inspection needs of many different materials.
Our Works
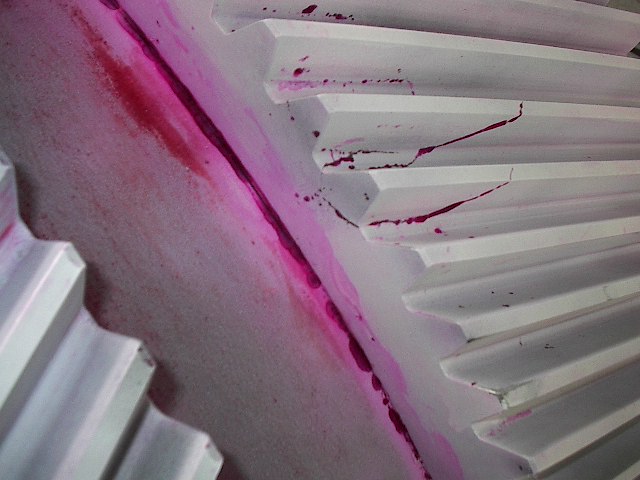
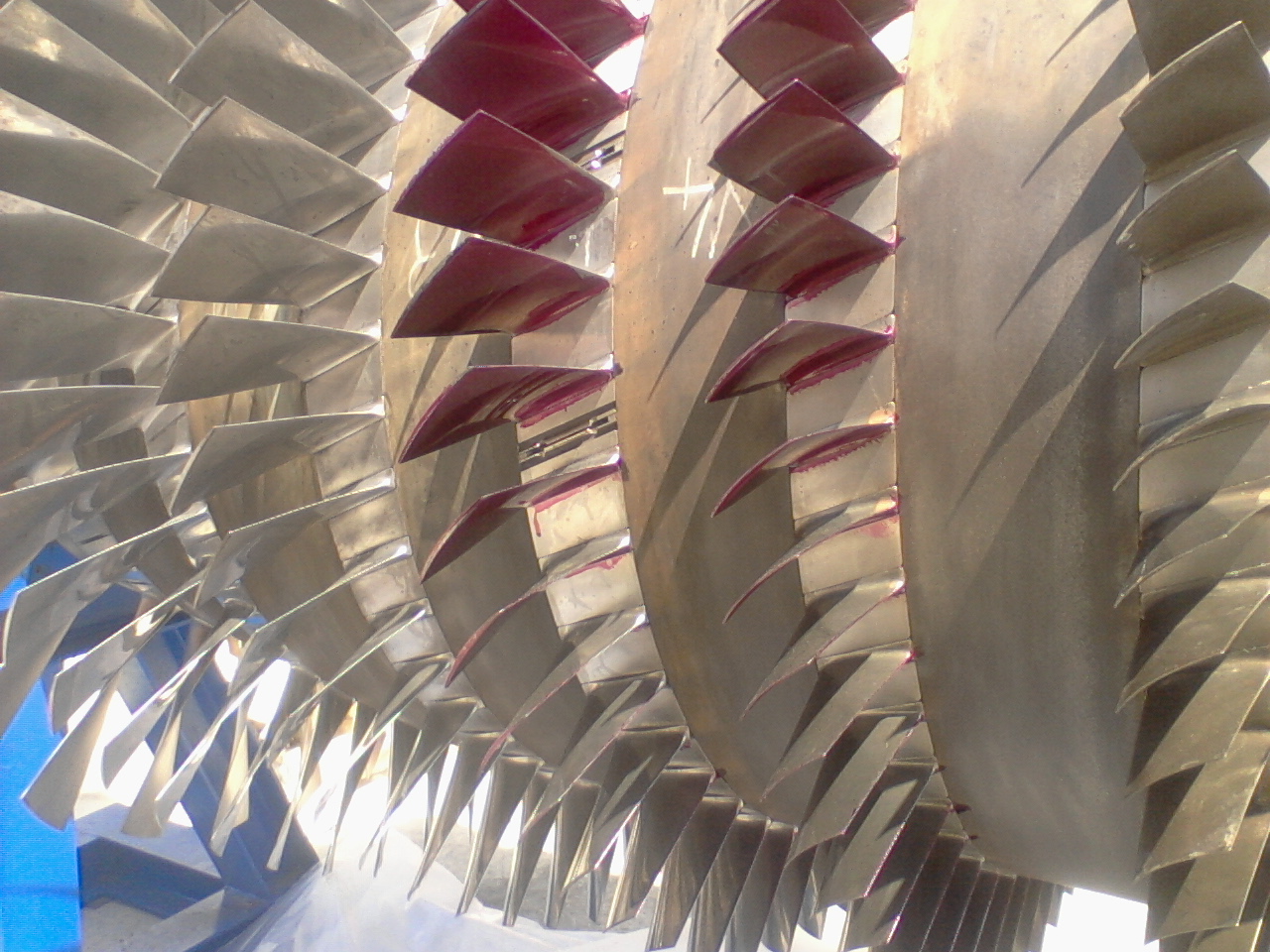
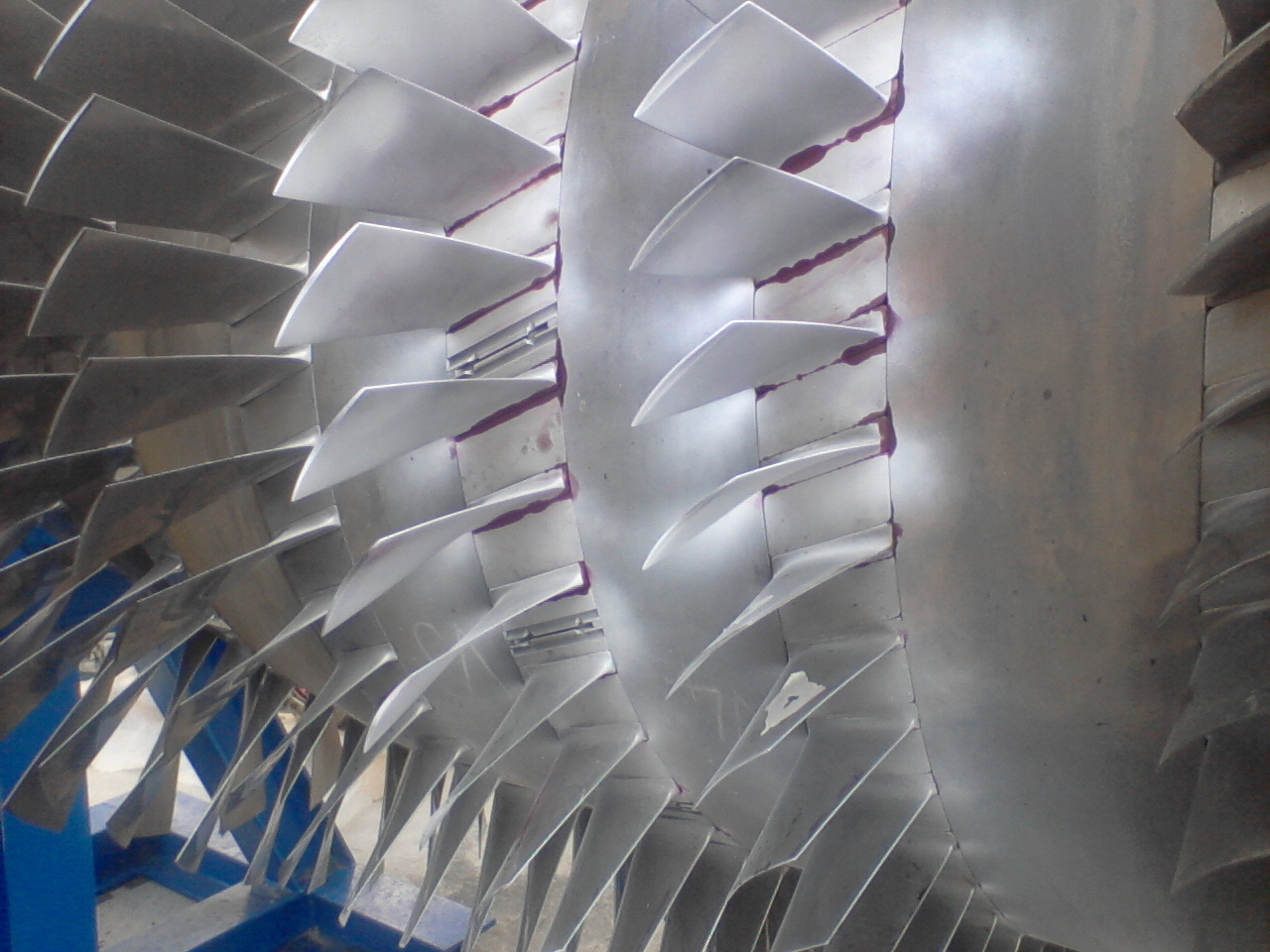
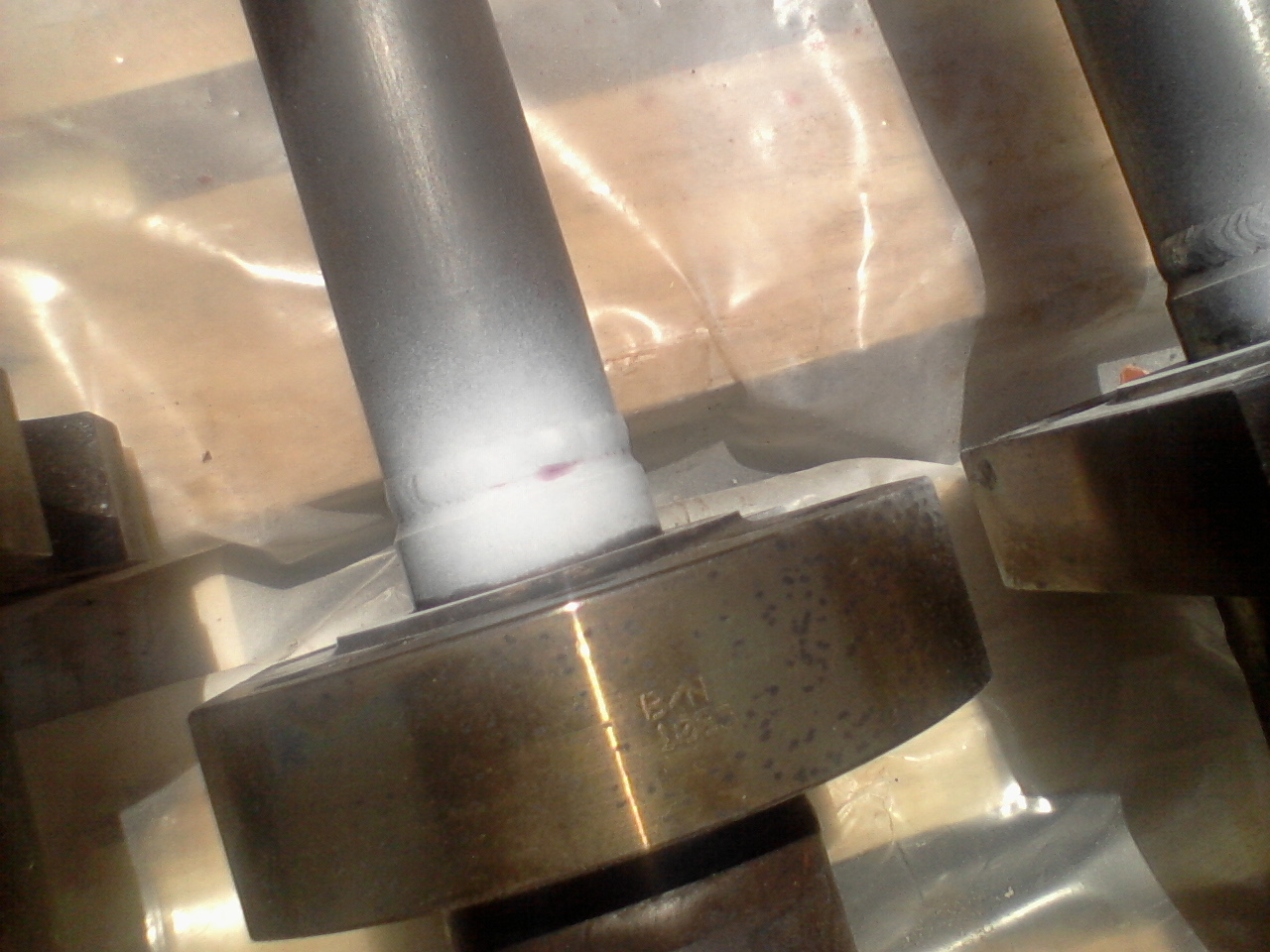
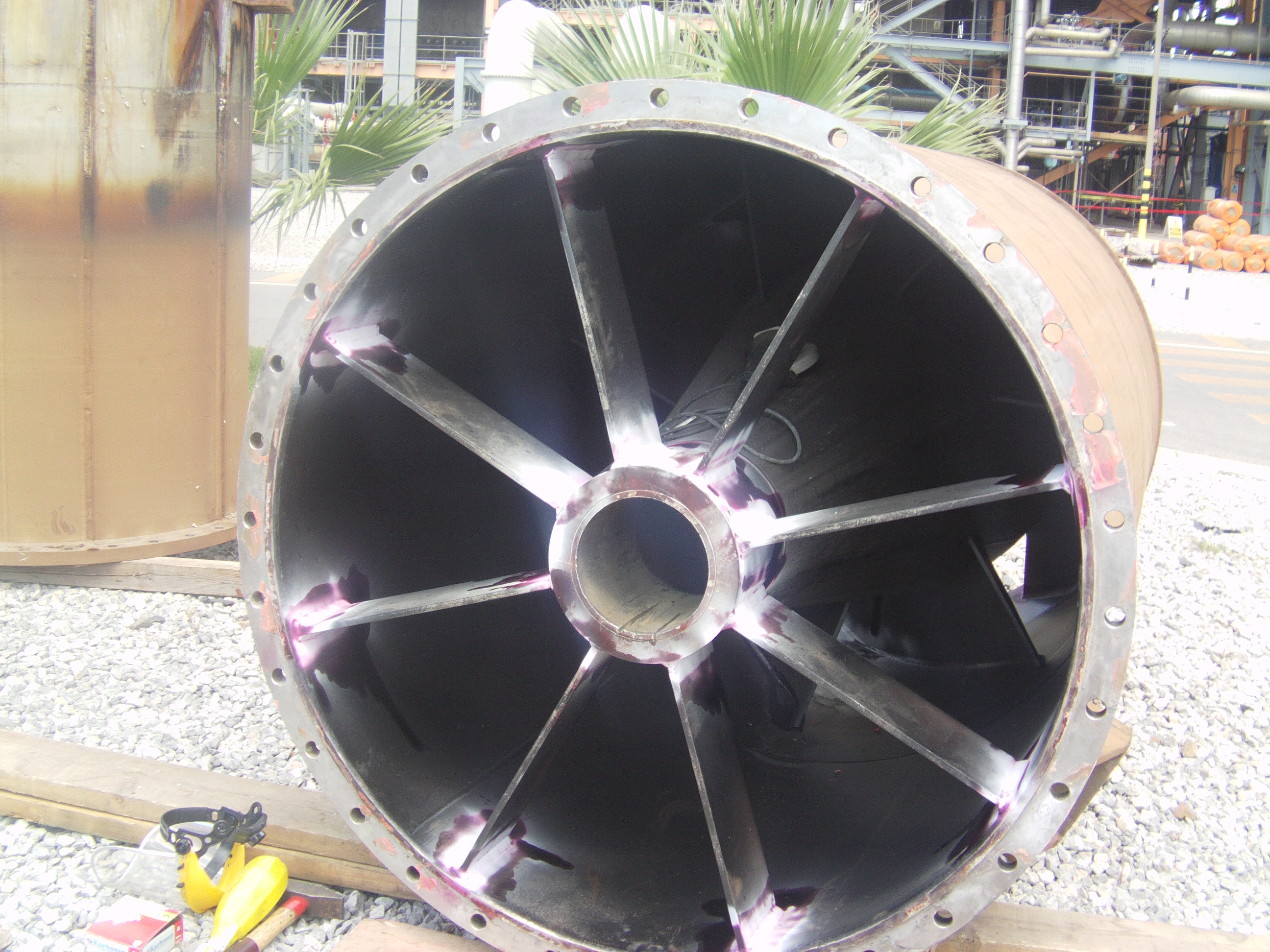
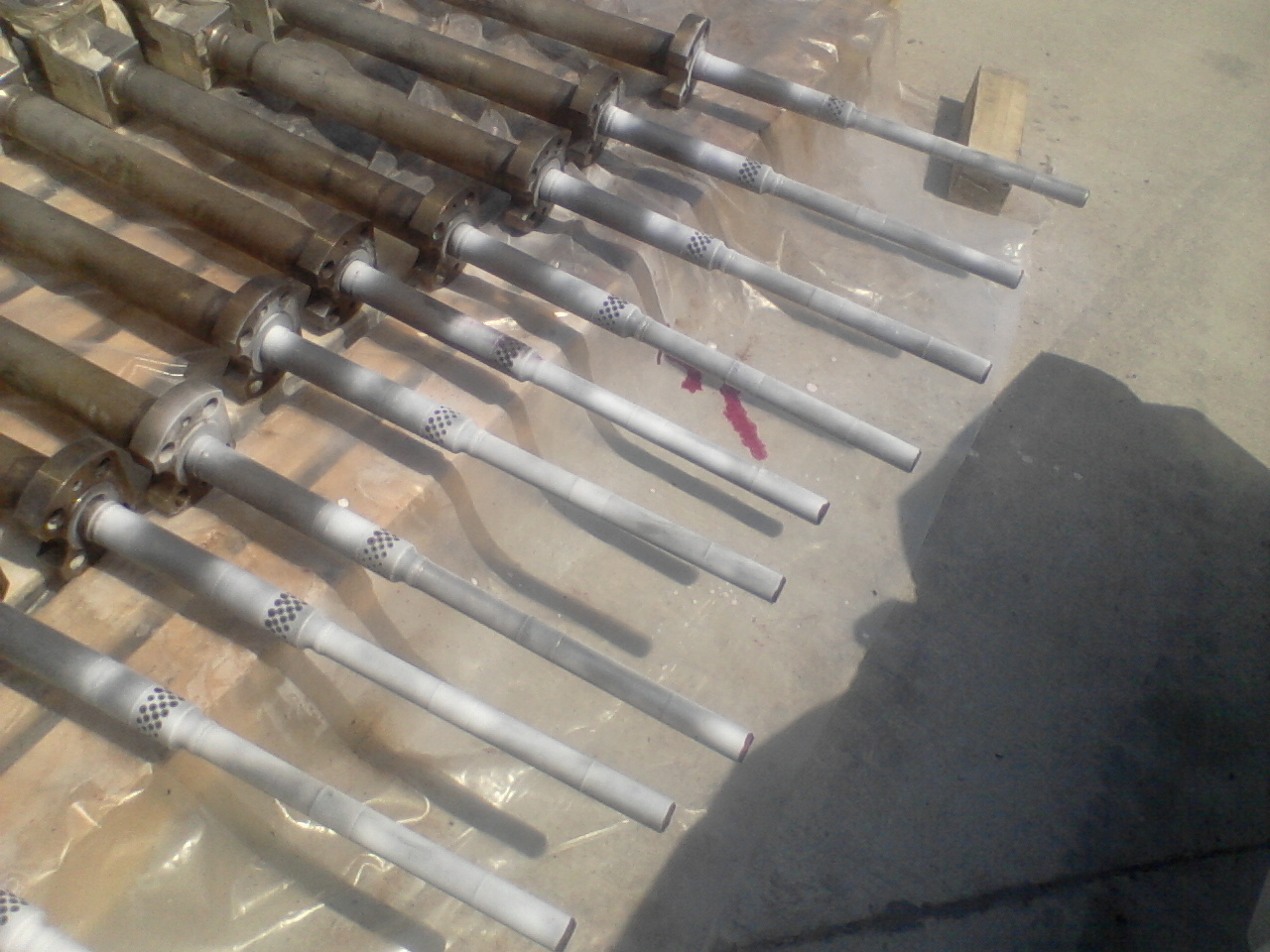
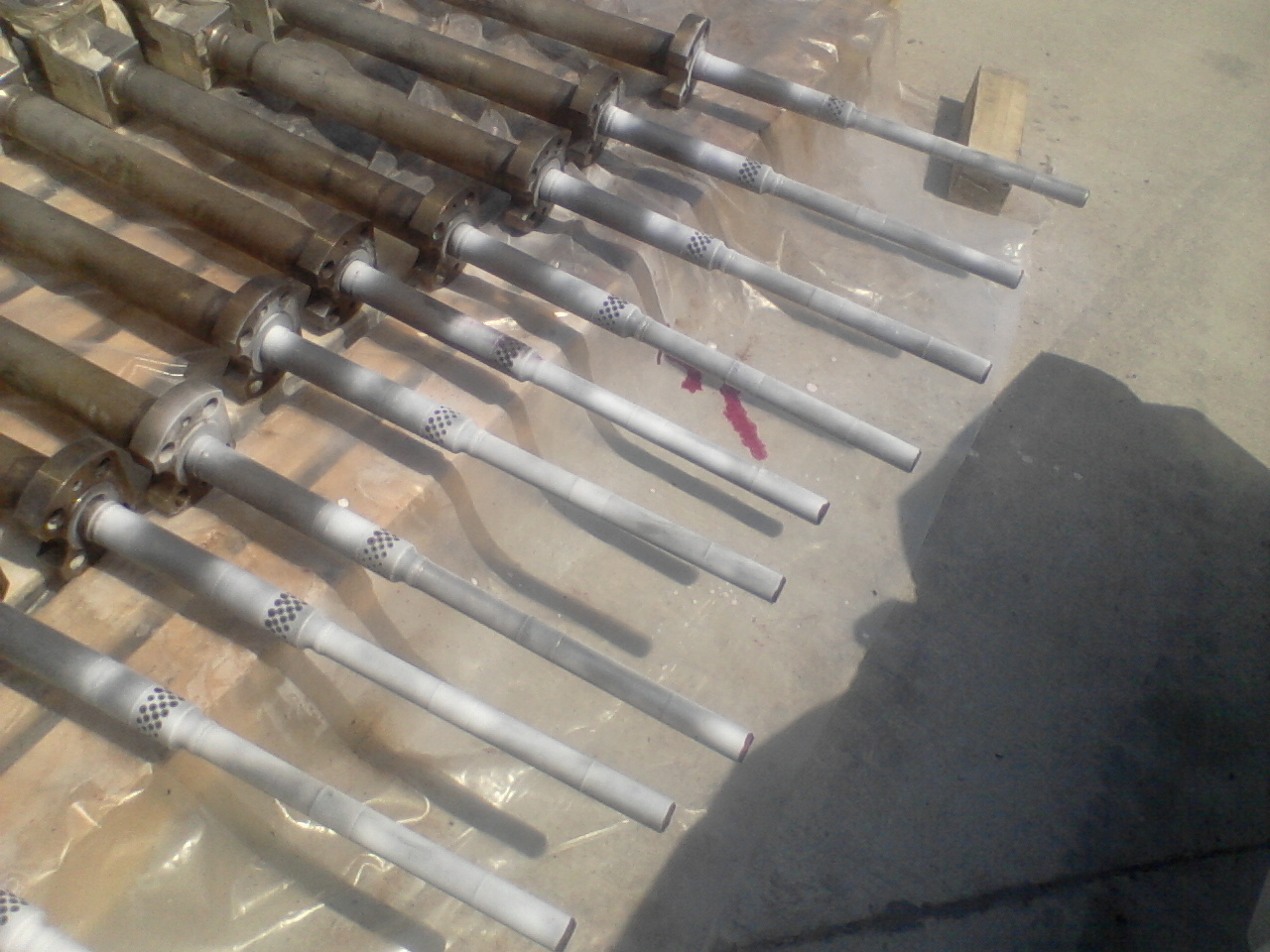
Application Areas
The main application areas of the dye penetrant inspection method are as follows:
- In welded manufacturing (pressure vessels, steel constructions, pipe manufacturing etc.)
- Stainless steel materials and welded fabrication
- Aluminum materials and welded fabrication
- Root cleaning in welded fabrication
- In casting manufacturing
- Processed surfaces
Application Process
The test surface is cleaned to remove any dirt, paint, oil, grease or any loose scale that could either keep penetrant out of a defect, or cause irrelevant or false indications. Cleaning methods may include solvents, alkaline cleaning steps, vapor degreasing, or media blasting. The end goal of this step is a clean surface where any defects present are open to the surface, dry, and free of contamination. Note that if media blasting is used, it may “work over” small discontinuities in the part, and an etching bath is recommended as a post-blasting treatment.
The penetrant is then applied to the surface of the item being tested. The penetrant is allowed “dwell time” to soak into any flaws (generally 5 to 30 minutes). The dwell time mainly depends upon the penetrant being used, material being tested and the size of flaws sought. As expected, smaller flaws require a longer penetration time. Due to their incompatible nature one must be careful not to apply solvent-based penetrant to a surface which is to be inspected with a water-washable penetrant.
After the penetrant is applied, a white developer is applied to the sample after the excess penetrant has been removed. Non-aqueous dry powder developer; It can be suspended in water and dissolved in water. Developer continues to be applied until it forms a translucent coating on the surface.
The inspector will use visible light with adequate intensity for visible dye penetrant. Ultraviolet radiation of adequate intensity, along with low ambient light levels for fluorescent penetrant examinations. Inspection of the test surface should take place after 10- to 30-minute development time, depends of product kind. This time delay allows the blotting action to occur. The inspector may observe the sample for indication formation when using visible dye. It is also good practice to observe indications as they form because the characteristics of the bleed out are a significant part of interpretation characterization of flaws.
The test surface is often cleaned after inspection and recording of defects, especially if post-inspection coating processes are scheduled.
Advantages and Disadvantages
The only disadvantage of the dye penetrant method is that the surface on which defects are to be detected should be smooth and very clean. On the other hand, there are no disadvantages in terms of cost and time factors.
- Cheapness – It is a relatively inexpensive method
- Ease – A portable non-destructive inspection method
- Dimensional Sensitivity – Very sensitive to thin and adjacent discontinuities
- Simplicity – It can be easily applied.
- Different Materials – It can be applied to many different materials.
- Productivity –Regardless of the orientation, all surface discontinuities can be detected by a process.